New technologies for predicting corrosion and modelling
03 August 2022
Full-field measuring techniques of wind blade working conditions
INEGI is developing a non-destructive testing system (NDT) which is intended as a first version of the final blade testing system to be developed in the coming months. The main results achieved include the definition and execution of NDT laboratory setups using DIC and IR solutions, the selection of the necessary equipment, as well as the development and successful use of the proposed trigger solutions.
Concerning the digital image correlation analyzes, two first approaches have already been carried out, namely the establishment of a system for evaluating displacements using static cameras with static blades, and them using static cameras with a rotating blade. For the defect detention system using thermography, several approaches were evaluated, and the most successful was found to be the use of an algorithm that does image comparison between thermographic images, one with a defect-free blade, used as a reference and one as the test subject.
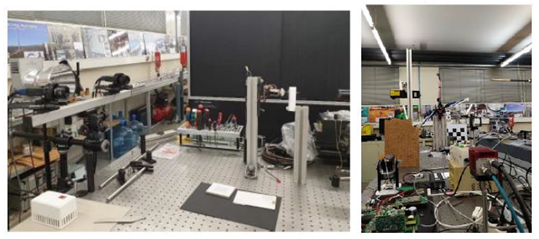
INEGI will continue with the presented plan and carry on with the remaining activities, especially with regard to the development using the structure from motion approach to carry out DIC analyzes with floating cameras, as well as with the establishment of the limits and strengths of the different thermographic approaches.
Implementation and assessment of FBGs/DFOs technologies
INEGI found that the materialization of several SHM laboratorial setups using both FBG and DFO technologies was successful, and validated the assumptions and decisions that were made, thus being ready to be implemented in the real-life scenario SHM.
Likewise, CETMA has shown the feasibility of FO distributed sensors to be applied as monitoring system in reinforced concrete structures. In particular, the developed SMART rebars (i.e., rebars with embedded FO sensors) show the following essentials points:
-
-
-
An SHM system based on SMART rebars with distributed FO sensors can provide thousands of sensing points that permits mapping of strain distributions the reinforcement of the structure.
-
The FO sensors provide the same results of traditional strain sensors in terms of reliability, with many advantages among which multiparameter measurements with the same sensor, no need of recalibration, easier wiring, high resistance in hard environment.
-
The developed embedding near surface technique of the FO sensors in the rebars is easy to realize and reliable; validation results on tensile strength test showed good behaviour.
-
The developed decoupling system permits to create segments of FO sensors not subjected to mechanical stresses.
-
The lab-trials related to the embedding process of SMART rebars demonstrated that the developed technique for the protection of the sensor in the inlet/outlet points of the FO cables both from the rebar and the concrete works properly; a 100% rate survival was achieved for all the typologies of concretes.
-
The lab trials related to mechanical tests on concrete elements with SMART rebars inside demonstrated the capability of the developed SHM system to properly detect different typologies of mechanical stresses (i.e., flexural, compression).
-
-
The activities developed will be used and furtherly implemented for SHM system for blade monitoring and concrete structures monitoring.
Modelling of GBS structure and influence of tested materials
INEGI finds as main results the definition of the design of the GBS and the study of the environmental conditions of the test site, as well as the numerical study of the structural forces on the GBS coming from the sea states and the transport and handling processes.
They also identified as the main next step to carry the planning and definition of the open sea test to be executed within the context of this project. Additionally, INEGI will continue to perform FEM simulation to study the structural integrity of the structure.
Development and validation of FEA model of composite structure for blades
The results from the MAREWIND Excel tool for the calculation of the transverse elastic and shear modulus show a better agreement with the available data using the Halpin-Tsai equations instead of the constant stress model. The MAREWIND tool has been validated for both the micro-mechanical and macro-mechanical part. Concerning the micro mechanical validation, good agreement with the reference results has been obtained. The Halpin-Tsai results are in excellent agreement with a negligible deviation.
The stress and strain calculated show excellent agreement with the reference results. Failure Analysis was performed with a unidirectional load in order to validate Tsai-Hill Failure Theory of Excel Tool and also in this case, the obtained results show an excellent agreement with the reference ones.
Likewise, the FE model tool has been validated for both the micro-mechanical and macro-mechanical part. For the macro-mechanical model, the deviations are smaller than 1% and therefore the experimental results of the literature and the numerical ones are in excellent agreement. Thus, both the micro- and macro-mechanical FE models can be considered validated.
The objective will be to use the high-resolution FE model of composite and tool to compare their results against the experimental data that will be made available by partners performing tests on the materials selected for the next phases of the project. The obtained results will be the basis for conducting the activities foreseen referred to the simulation of the blade prototype (or part of it) predict the fatigue life of the wind turbines.