Over the last four years, the MAREWIND partners from leading industry, technological and research organisations have delved into the exploration of new materials, gathered experimental data, and created predictive models. These efforts aim to enhance the durability, minimise maintenance requirements, and reduce environmental impacts in the offshore wind energy sector.
Explore the results of the MAREWIND project!
The MAREWIND adventure has reached the end, and it is logic that this evokes certain sensations, mainly coming from the initial stages of the project. For Lurederra team, assuming the coordination of such a complex project, combining various different and specific technologies implied a challenge, but also excitement for such interesting research.
In a simultaneous way, progress was expected in functional nanocoatings, in novel concretes and in alternative composite formulations for blades, as well as in relation to advanced Structural Health Monitoring systems, including both internal and external strategies.
We knew that certain control was necessary in all development fronts, so sometimes we needed to juggle the tasks of the active work packages with the periodic revisions and compilation of documents.
Nevertheless, the overall feeling after four years of project is gratifying thanks to the fruitful collaboration, the high expertise of the partners and to the hard-working spirit of the consortium to fulfil all the activities.
Finally, we hope that the relevant results of the project are soon successfully integrated in offshore windmill structures, promoting the cost reduction and improving the management of resources regarding renewable energies.
Lurederra team Coordinator of the MAREWIND projectOver the last four years, the MAREWIND partners from leading industry, technological and research organisations have delved into the exploration of new materials, gathered experimental data, and created predictive models. These efforts aim to enhance the durability, minimise maintenance requirements, and reduce environmental impacts in the offshore wind energy sector.
The MAREWIND project has developed specific functional coatings, advanced concrete formulations and novel composites as well as monitoring technologies that not only push the boundaries of functionality but also prioritise sustainability. The advancements have been done in various areas, each contributing to the overall progress of offshore wind materials.
The anti-corrosion coating, applied to the W2Power Floating Structure located in the Canary Islands (Atlantic Ocean) has shown no signs of corrosion, proving the effectiveness of the solution for future applications. Additionally, the anti-corrosion coating solutions have also shown significant advancements when focusing on repairing critical turbine components, treating vulnerable areas, and targeting the most at-risk sections.. One of the main advantages of the mentioned protective coating, implies direct application by spraying, but also, the compatibility with paints required by marine visibility regulations.
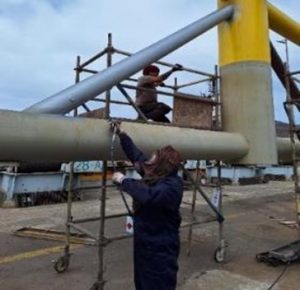
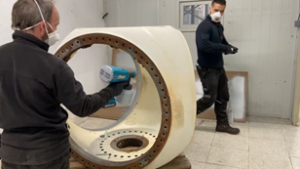
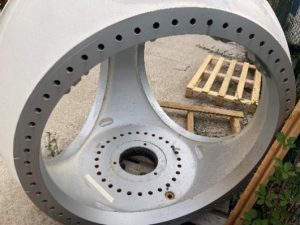
Turning to the antifouling coating, the assessments of samples submerged in Sines (Portugal), as part of the Gravity-Based Structure (GBS), have revealed the unique attributes of the low-thickness product. These tests demonstrate its superior adhesion when compared to commercial alternatives, showcasing its potential for enhanced performance. In parallel, other antifouling coatings are undergoing tests in the Mediterranean waters at “Observatoire Océanologique de Banyuls-sur-Mer” to further expand our research and results.
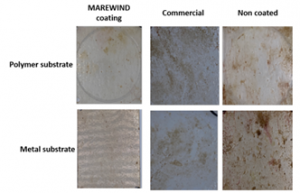
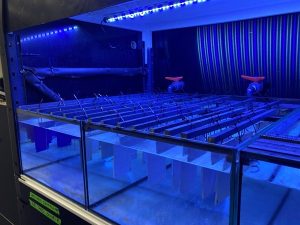
The results of the test carried out, showed clear antifouling effect for the MAREWIND coating after 7 months of exposure, and even better performance, compared to commercial benchmark. The tests included not only visual inspection, but also biofouling monitoring by mass and surface concentration of chlorophyll a.
Additionally, treated coupons embedded in frames with anticorrosion and antifouling coatings have been installed in offshore wind farm in Teesside (North Sea). These frames are positioned across three different exposure zones: the subsea zone, atmospheric zone, and intermediate splash conditions. Over the course of the project, various inspections have been run to assess the performance and durability of these innovative coatings.
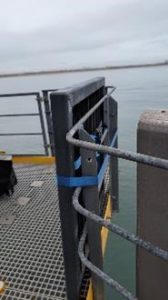
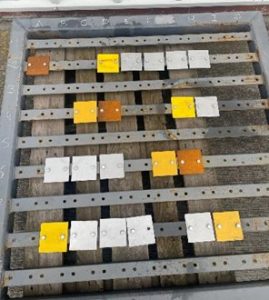
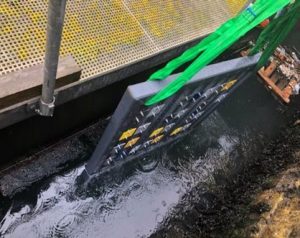
Test conducted across atmospheric, splash zone, and subsea conditions
The first analysis carried out showed no corrosion on the MAREWIND samples for both atmospheric and splash zones after 6 months of exposure. Next, the newly developed concrete formulations offer enhanced durability and improved sustainability for offshore environments. On the one hand, the Ultra High-Performance Concrete (UHPC) is expected to outperform current commercial options, offering a durable, preventive solution during production. It also shows strong potential for maintenance and repair applications, where its durability and resilience can extend the lifespan of structures in demanding environments. Currently, real exposure tests are ongoing in Gijón Harbour.
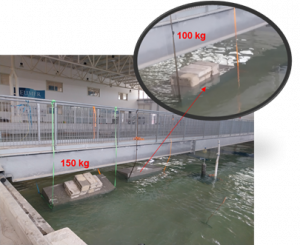
On the other hand, the project has developed sustainable and cost-efficient concretes based on Alkali-Activated Materials (AAMs) that demonstrate durability, excellent flow capacity for molding, and strong resistance to freeze-thaw cycles. Suitable prototypes were manufactured with both concrete technologies, validated at real exposure in subsea conditions (AAM in GBS in Portugal).
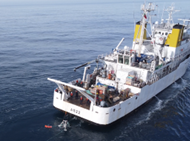
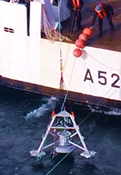
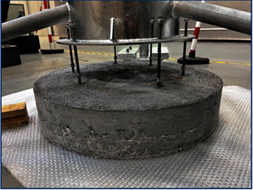
GBS in Sines (Portugal). Analysis after 6 months exposure in the GBS submerged in Sines.
Additionally, the project has successfully produced a 13-meter blade using an innovative composite technology from recyclable resin, incorporating a circular sustainable design, and including validation by mechanical tests in CTL (Galway). By combining these advanced materials and Structure Health Monitoring technology, the project enhances resource management and structural integrity in offshore infrastructure.
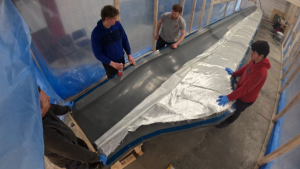
Key improvements include the integration of Fiber Reinforced Polymer (FRP) bars in novel concrete formulations within innovative concrete formulations and the embedding of Fiber Optic Sensors across blades, gravity-based structures (GBS), and concrete structures. Additionally, external blade inspections conducted with advanced drones provide a comprehensive view of structural condition.
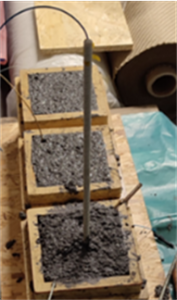
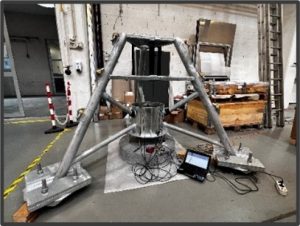
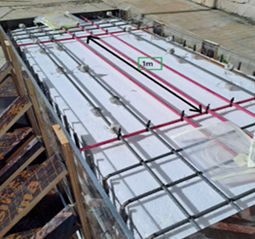
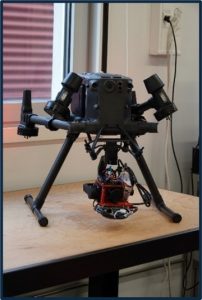
Hosted at ACCIONA Construction and facilitated by PNO Innovation Belgium and PNO Innovation (Spain), the workshop was a resounding success with over 100 participants attending both online and in person.
The event showcased key highlights that underscored the advancements and future direction of the offshore energy sector. Participants gained valuable insights from professionals on evolving landscape and opportunities within the future of the offshore energy market.
Expert presentations on cutting-edge innovations in durable and sustainable materials, highlighted their role in advancing on offshore infrastructures. Additionally, the event showcased solutions designed to align with the EU’s 2050 climate neutrality goals, driving progress in offshore sustainability.
Explore the final results of the project:We’re thrilled to announce that the European Welding Federation (EWF) is now a liaison member of ISO/TC 35 Paints and Varnishes!
This prestigious recognition comes as a result of the incredible work developed on the MAREWIND project.
This collaboration marks a significant step forward in enhancing standards and fostering innovation within the industry.Together, we aim to achieve greater quality and performance in paints and varnishes, benefiting professionals and consumers alike.
Stay tuned for more updates as we embark on this exciting journey!
Further information here.The MAREWIND project started in December 2020 and today is one step further to deliver a real value proposition for the future of the offshore wind energy. On the one hand, the technical results already collected, have validated the key technological developments regarding protective coatings, advanced concretes and innovative recyclable composites. On the other hand, the modelling tools developed are showing relevant conclusions including predictive data for corrosion evolution as well as suitable identification of on-site defects regarding Structural Health Monitoring systems. Moreover, the first conclusions regarding LCA show important environmental advantages for the different developments, so this final stage of the project is expected to be full of highlights.
On December 2023, the MAREWIND project achieved a significant milestone by deploying the Gravity-based structure (GBS) in open sea. Collaborating with the Hydrographic Institute from Portuguese Navy, the GBS was successfully deployed in Sines (Portugal). In July 2024, the GBS will be retrieved from the seabed to conduct an analysis of the results.
Additionally, Enerocean provided data from experimental work including real exposure tests that has been used for feeding the modelling carried out by Idener. In this context, MAREWIND has performed real scenarios simulation in Teesside and Canary Islands, where the protective effect of coatings was evaluated as well as the impact of the climate change over the next 40 years.
At this stage, the real exposure tests of the anticorrosion and antifouling coatings have been already launched in Teeside (North sea) and Banyuls-sur-Mer (Mediterranean sea), Sines Portugal and Canary Island (Atlantic sea). Thus, EDF, Inegi and Enerocean are supplying the various specilised structures needed to conduct the tests: windfarms, GBS, and floating platform, respectively. Furthermore, Koskhil is focusing on repair and maintenance operations, applying anticorrosion coatings to various turbine components and monitoring their effectiveness. The project is moving forward with the aim to solve the technological, economical, business, and societal challenges Europe is facing today. Its innovative solution will establish technological base for competitive offshore wind farms constructions, exploitation, and maintenance in Europe.
Why did you join the MAREWIND project and what’s your role?
ENEROCEAN joined the MAREWIND project because it is crucial for us to be involved in projects that address key topics to enhance the competitiveness of renewable offshore energies. Thanks to the MAREWIND project, EnerOcean takes part in the development and testing of cutting-edge technologies in materials durability and maintenance, which contribute to the decrease of the O&M and CAPEX costs of renewable energies offshore structures, such as our W2Power floating offshore wind platform.
In the MAREWIND project we act as “final user”, contributing our experience and perspective throughout its duration. More precisely, we lead several sea testing campaigns of novel antifouling and anticorrosion coatings, putting our experience on sea testing campaigns.
Could you elaborate on your involvement in the demonstration of the technologies developed in the project?
During the first part of the project, we performed sea testing campaigns on coupon and mid-scale samples in the testing sites PLOCAN and TECNALIA. This included flat samples but also some dog-bone like samples (for fatigue analysis of the anticorrosion coatings) as well as part of real components such as mooring lines and cables.
At this stage we are performing large-scale demonstration of the antifouling and anticorrosion coatings by applying them on the W2Power floating structure that was subsequently deployed at sea. It is worth mentioning that this prototype was the first floating wind prototype deployed in the open sea in Spain and it is currently one the few functional floating wind prototypes in Europe.
How do you see the future of the MAREWIND project?
We believe that the MAREWIND project can have a great impact both on the offshore and wind industry. From our point of view, the future of MAREWIND project is highly dependent on the success of the products that have been developed and tested within the project. With respect to the antifouling and anticorrosion coatings, the project has shown its great performance and potential, however, sometimes the offshore industry is reluctant to changes, so the first barrier is the entrance and subsequent penetration into this market. To overcome this, it is crucial for end-users to be confident that our products have undergone rigorous real-world testing, received certification from a well-known third party, and feature a straightforward, standardized application process on large structures.
READ MORE ABOUT ENEROCEAN HERE.
Why did you join the MAREWIND project and what’s your role?
The European Welding Federation (EWF) joined the MAREWIND project because it aligns perfectly with our strategic objectives, particularly in the maritime sector, which is a key focus area for us. Our primary role within the MAREWIND project is to contribute to the standardisation activities. This involvement is crucial, as it ensures that the innovations and advancements developed through the project meet rigorous industry standards and can be seamlessly integrated across the maritime sector.
What specific methods or strategies will be employed to ensure that the standards and regulations mapped are effectively integrated into the project’s outcomes?
To ensure that the standards and regulations are effectively integrated into the MAREWIND project’s outcomes, we have adopted a meticulous and comprehensive approach. The first step involved developing a standardisation activities strategy and roadmap.
Initially, all partners contributed to identifying relevant standardisation documents, bodies, and technical committees. As the project progressed, we focused on applying these documents and pinpointing gaps between the existing standards and the project’s technological developments.
Currently, we are actively engaging with standardisation bodies to report our findings and coordinate the next steps. This ongoing interaction ensures that our project’s innovations are aligned with industry standards and can be widely adopted.
How will the consortium integrate the focus on EU standardisation and regulation to support the achievement of the MAREWIND project?
The consortium’s integration of EU standardisation and regulation is pivotal to the success of the MAREWIND project. The EU’s emphasis on standardisation and regulation within research and development projects is a commendable initiative. It serves as a bridge, promoting the transition of groundbreaking technological advancements from the project phase to industry-wide application.
By adhering to these standards and regulations, we ensure that our innovations are not only cutting-edge but also compliant with the highest industry benchmarks. This alignment facilitates the seamless incorporation of new technologies into standardisation documents, ultimately driving industry progress and adoption.
Can you elaborate on the planned stages and phases for standardisation activities within the project, and how these activities will be coordinated with the work carried out under the various WPs?
The standardisation activities within the MAREWIND project are meticulously planned and executed in several stages to ensure thorough integration and coordination with the various work packages (WPs). The provided schematic illustrates this detailed roadmap.
- Standards Mapping Report: This initial phase involves creating a comprehensive standards mapping report serving as a foundation by identifying existing standards, standardisation documents, relevant bodies, and technical committees that align with the expected project outputs.
- First Standardisation Search Methodology: During this phase, the focus is on expected project outputs. Partners collectively identify existing standards, those under development, and finalise relevant standards. This phase ensures that the project results are aligned with existing frameworks.
- Identification of Standardisation Gaps: As the project progresses, a detailed analysis is conducted to identify gaps between the existing standards and the technological developments from the project. This step is crucial to pinpoint areas that require new or revised standards.
- Second Standardisation Search Methodology: With a focus on the results, this phase further refines the search methodology to ensure that all relevant standards are identified, considering the technological advancements achieved.
- Standardisation Bodies Engagement: This ongoing process involves active interaction with standardisation bodies to report findings, articulate the gaps, and coordinate the next steps. Key questions addressed include which bodies to engage with, how to approach them, and the appropriate timing for engagement.
- Recommendation Document: The final phase involves drafting and submitting a recommendation document. This document compiles all findings and recommendations and is submitted to relevant working groups within CEN (European Committee for Standardisation) and ISO (International Organisation for Standardisation).
By following this structured roadmap, the MAREWIND project ensures that its innovative outputs are seamlessly integrated into industry standards, thereby promoting broader adoption and compliance across the maritime sector.
How do you see the future of the MAREWIND project?
We see a bright and promising future for the MAREWIND project. With its innovative approaches and cutting-edge technologies, the project holds great potential for transformative applications in the offshore and maritime +sectors. By addressing key challenges and advancing state-of-the-art solutions, MAREWIND is poised to significantly enhance efficiency, sustainability, and resilience within these industries.
Why did you join the MAREWIND project and what’s your role?
PNO Innovation was invited to participate in MAREWIND and gladly accepted the challenge to offer the company’s consultancy services and well-established expertise to the project’s benefit. The main target of MAREWIND is to develop advanced durable materials and recyclable solutions which reduce materials use contributing to the European Union’s climate goals. This is in line with our commitment at PNO to support various stakeholders elaborating innovative solutions to tackle the challenges that the energy sector is facing. Furthermore, our proficiency in communication, dissemination and exploitation activities enabled us to confidently take the lead in establishing and executing a strategic plan for identifying and engaging with key stakeholders in the energy and other markets.
As market leader in subsidy and innovation advice, what are your ambitions in contributing to the European renewable energy targets?
PNO actively supports numerous companies in developing their ambitions and actualising their technology roadmaps for the future. By identifying transformative innovations that reshape their operations and conceptualising innovative projects centred around strategic technologies and markets, we help pave the way for their success. To release this vision, we leverage over 500 available public funding mechanisms across Europe, to support our clients in creating industrially driven innovative projects and concepts.
Moreover, we are committed to providing strategic advice that encourages the adoption of sustainable practices, ultimately facilitating the sector’s transition towards greener and more efficient operations. Our goal is to play a pivotal role in facilitating positive change, helping businesses thrive while minimising their environmental impact.
PNO is leading Communication and Dissemination activities within the MAREWIND project. How would you assess the significance of reaching the public audience to showcase the importance of a more efficient and renewable energy system?
We believe that reaching the public audience is crucial on multiple fronts. Firstly, engaging the public fosters awareness and help supporting sustainable practices and standards. Secondly, policymakers can be influenced by this public support, playing a key role in shaping a favourable environment for new innovative initiatives that drive a more sustainable and durable wind energy sector. Additionally, these actions can encourage wind energy industry to adopt and promote sustainable practices.
In summary, reaching the public audience not only raise awareness but also catalyses a collective effort towards a more sustainable society and efficient industrial landscape.
Given the technical nature of the project, how do translate complex information into clear and accessible messages for both industry experts and the broader public?
Our approach involves a strategic translation of complex information into clear and accessible messages tailored for both targeted groups. We employ different tools including simplified visualisations and articles with less-technical language. For example, for a wider audience we draft public-facing materials using simple terms and emphasising the project’s significance and benefits in a related manner, while for industry experts, we provide in-depths technical documentation. This approach aims to bridge the gap between technical and complexity from one side, and accessibility from the other side, reaching several targeted groups.
How would you explain to a wider public what will be the impact of the MAREWIND project?
The primary difficulty with the offshore wind structures is the durability of the materials and maintenance which consequently imply failures, misfunctioning, loss for efficiency in energy generation and which have a major repercussion on O&M and CAPEX. MAREWIND is expected to highly impact the EU wind energy industry, which is projected to have the largest contribution to the renewable energy targets for 2030. It will strengthen the European leadership position in the industry as well as optimise the sector. Moreover, it will help reduce Europe’s energy dependance and thereby delivers significant macroeconomic benefits.
How do you see the future of the MAREWIND project?
The MAREWIND project is set to significantly impact the future of the European energy sector by making offshore wind turbines more efficient, durable, and cost-effective. One major impact of MAREWIND’s innovations is the reduction in the Levelized Cost of Energy (LCOE). By extending the operational lifespan of wind turbines through advanced antifouling and anticorrosion coatings, the project reduces the frequency of maintenance and repairs. This means that wind farms can operate more consistently and at higher efficiency, leading to a lower overall cost of electricity production. Moreover, the use of carbon-reinforced composite materials for wind turbine blades will make the turbines lighter and more efficient. This reduction in weight will decrease the mechanical strain on turbine structures, enhancing their efficiency and longevity. As a result, energy production becomes more reliable and cost-effective, contributing to a more stable and affordable energy supply.
In summary, the MAREWIND project will significantly lower the costs associated with offshore wind energy, enhance the reliability and efficiency of wind farms, and position offshore wind as a leading source of renewable energy in Europe. These impacts will drive the growth of the offshore wind sector, contributing to Europe’s transition to a sustainable and economically viable energy future.
READ MORE ABOUT PNO HERE.
Why did you join the MAREWIND project and what’s your role?
RINA Consulting joined the MAREWIND project to face the challenge of developing and validating new materials for the wind offshore sector. Our team has been involved in two main areas: sustainability assessment and predictive modeling with Finite Element model (FEM) Analysis.
How does RINA plan to support the technical validation activities for the results of MAREWIND, ensuring compliance with environmental, economic and social impact assessments?
Within MAREWIND, RINA plans to support the technical validation activities for the results of the project by leading a comprehensive evaluation across three key pillars: environmental, economic, and social impact assessments. Our main goal is to ensure that all assessments are iterative and integrated from the early stages, with primary data provided by our project partners and supplemented by reliable secondary sources when necessary. This approach guarantees a holistic and robust validation process, aligning with the project’s sustainability goals.
Additionally, we will integrate the results across the three key pillars, in an overall assessment, to determine the global sustainability performance of developed solutions, compared to conventional technologies.
Can you elaborate on the specific methodologies and approaches that RINA will employ in conducting the environmental, economic and social impact assessments for the project results?
RINA has a long experience in Life Cycle Thinking approach, i.e. a set of three different methodologies assessing the environmental (LCA), economic (LCC) and social (S-LCA) performances of a product or a service along its life cycle. In the framework of the MAREWIND project, the innovations are examined at turbine and product level, setting a comparison with the commercial references. The three comparative analyses cover the whole life cycle of the products, from their production to their disposal, from the different perspectives, giving as outcome the environmental impacts, costs, social risk of new solutions.
In what ways will RINA be involved in modeling and predicting the response of composite structures for blades to various environmental conditions? Can you discuss any innovative techniques or tools that will be utilised in this process?
In this context, we determined the material properties for the analysis through the development of an analytical design tool and Finite Element (FEM) models. Specifically, two FEM models were created: the first to validate the characteristics of the chosen material, and the second to support the design of the complete wind blade, considering the specified material and composition.
For predicting fatigue life, we are developing a custom methodology utilising ad hoc Python scripts in combination with the finite element model. Initially, the classical lamination theory was used together with a cumulative fatigue damage model, to forecast the stiffness degradation of the composite material over each fatigue cycle. To enhance the accuracy of fatigue life predictions, the results from the analytical approach are integrated with the finite element model of the blade.
What challenges do you anticipate in conducting the technical validation activities and modelling for the project, and how does RINA plan to overcome these challenges to ensure accurate and reliable results?
For sure, the innovative products could express particular materials composition that should be properly modelled in our analyses, as well as the low TRL of the technologies could affect the results for energy consumptions and related costs. For these reasons, we need to pay particular attention in the comparison with benchmark commercialised products, in order to make it as fair as possible.
Furthermore, effectively capturing the behavior of composite materials through modeling and ensuring the accuracy of analytical methods and finite element models present challenges. To ensure reliable results, RINA plans to address these challenges by implementing rigorous validation techniques, leveraging advanced simulation tools, and collaborating closely with partners and subject matter experts.
How do you see the future of the MAREWIND project?
MAREWIND products proved to have good sustainability and technical performances over the different modeling and validation assessments performed along the project. Their results are promising for a future distribution on the market, after a proper scale-up and technical improvement of their production process. These products could have an important role in the shifting towards a more sustainable wind-offshore sector.