The MAREWIND project as leader towards a more sustainable and circular offshore wind sector
15 February 2023
During the last months, the MAREWIND project has made great strides towards the validation of the developed samples. At present, the natural step is the validation in a real environment where formal controlled testing will be performed to ensure that the materials developed satisfy the expected requirements.
The consortium has started the work in real exposure and also with samples with real materials and morphologies, enabling relevant validation.
On the one hand, for bigger pieces, TECNAN has defined key parameters – such as flow rate, speed or distance – of spray gun application, and characterised the resulting samples with the aim to compare its properties versus the ones previously validated in the laboratory. Several application tests were carried out in order to adapt the procedure to complex and more realistic morphologies. More in detail, real pieces of mooring lines and inter array cables have been coated with the antifouling solution via spray gun, maintaining all the expected repellence properties, as in previous tests. The anticorrosion coating was also applied on samples around 1m2 and with curved and complex geometries with no imperfections observed. Besides, TECNAN has optimised strategies for removing the excess of product and curing conditions for real fastening elements regarding dip-coating application.
On the other hand, TWI for its side is improving the application of the superhydrophobic coating for blades for improved control and for having higher resistance to mechanical impact.
Additionally, as advanced concrete-based materials concerned, ACCIONA has made preliminary UHPC floating prototypes, focused on the relevant scale prototype design that will be tested in more realistic environments such as wave basin for offshore application studies (EUMER facilities), at the same time, real exposure durability testing will be performed at ACCIONA Habour demo-site. Furthermore, for the Alkali Activated Concretes (AAC), CETMA carried out a small-scale prototype with a complex geometry to evaluate the ability of the AAC to flow within the mould. They have also designed the final prototype indicating the number and position of SMART reinforcing rebars.
Advances concerning the blade prototype, imply that EIRE has been working on the validation demonstrator, testing the 5m wind blade spar box, as representative section of the main structural component of the 13 m blade.
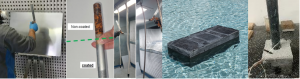
As part of the validation activities, final optimisations of the selected formulations are being carried out in order to maximise the properties of the novel solutions developed.
More in detail, TWI has started the optimisation of the best performing coating formulation, working on the 3rd generation of antierosion coatings adjustment. After several tests, TWI has adjusted the level of functionalized microparticles in the formulation, showing an increased wear resistance of the coating. For the reinforced composites formulations for blades, the contemplated strategies by TWI and CETMA, are progressing properly. Respecting the work of TWI, the final material test campaign for GF/epoxy-SiO2 as the new blade material was completed. The results are compared with conventional GF/epoxy, showing that the modified epoxy-SiO2 resin outperforms the conventional epoxy resin in the majority of property tests. CETMA for its side, is working on the infusion process of the TPR (thermoplastic reactive resin), as a new recyclable resins. The results of testing campaign for GF/TPR as the new blade material, has showed that properties of recyclable composite are comparable with conventional GF/epoxy laminates. They have defined the final composition, layup and geometry of the full TPR demonstrator, and as regards TPR matrix, CETMA has selected a specific recyclable resin to be used in scale up activities with low exothermic properties to produce large parts with thick sections.
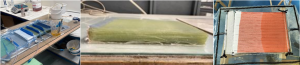
The scale-up of formulations includes the progress regarding liquid nanocoating production as well as novel concrete or composite fabrication.
On the one hand, production of the anticorrosion and antifouling coatings started with first batches of 20 liters with suitable results, having the focus on the 100 liters target of production. The spray gun application and the monitorization of the key parameters (viscosity, particle size…) showed that the larger batches have the same tendency as the product made at laboratory scale. As a result, TECNAN will produce larger batches following the same parameters. In addition, INL is producing the self-healing active material for the anticorrosion system, and studying what is the most suitable format for the scalability.
Also, the preparation of pilot batches of SiO2 mixed with epoxy infusion resin (epoxy-SiO2) has already started by TWI side, in order to supply EIRE for the production of the new blade reinforced composites
.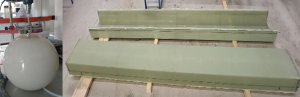
After having performed all laboratory tests, the MAREWIND project is currently gradually moving to a real environment.
Currently, TECNAN is testing the bigger pieces in saline mist chamber before preparing the ones to be exposed to real conditions. Specific and bigger samples coated with the anticorrosion system are envisaged to be tested by ENEROCEAN in the upcoming months in real marine environment using TECNALIA’s HarshLab floating laboratory. On the other hand, ENEROCEAN is currently testing the antifouling coatings on flat panels, both partially submerged and in total immersion, as well as on real samples (moorings and cables) in real marine environment. These antifouling coatings tests are being performed at the Oceanic Platform of the Canary Islands (PLOCAN) facilities.
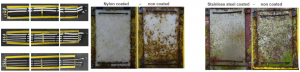
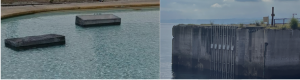