Development of anticorrosion coatings for metallic elements
03 August 2022
During the first 18 months of the project, the MAREWIND Consortium has been working on the development of an anticorrosion coating for key metallic elements. The coating consists of three layers with different chemical compositions and, therefore, different corrosion protections. Moreover, the multilayer system has been developed layer by layer:
-
Layer 1 has a metallic composition providing the substrate with a good cathodic protection. Considering the low curing temperature and stability overtime, two main matrix formulations were investigated, as well as various metallic components and loads.
-
Layer 2 incorporates a self-healing system based on core-shell micro/nanofibers. Nanofibers were produced and optimized regarding viscosity of each material and prepared by electrospinning technique. Then, they were completely characterised in terms of textural, morphological and chemical properties, revealing an increase in corrosion protection close to 40 times.
-
Layer 3 was designed as an Organic Inorganic Hybrid (OIH) sol-gel matrix with reinforcements of fibres and ceramic nanoparticles. The formulation has been adapted and optimised to provide the coating with additional properties such as increased mechanical strength and hydrophobicity to protect even more the target metallic offshore structures.

Different systems were proposed regarding matrices and curing procedures at low, medium and high temperature. Also, an exhaustive work regarding coating application methods as well as the characterisation of coated samples has been performed. With these results, finally the system of anticorrosion coating has been achieved in low temperature strategy.
Coating application systems
Two strategies were designed for this purpose:
- Application via spray gun:
A suitable procedure depends on the adjustment of the spray gun parameters to obtain uniform and smooth coatings. TECNAN was able to generate a reference protocol for each layer defining main parameters involved in the application process such as atomization pulverization, flow rate.
- Application via dip coating:
Dip coating is more appropriate for applying the coatings on a large number of small metallic elements. A small-scale device has been designed for a preliminary adjustment of the coating application.
The results show that spraying is the main alternative, since it provides a good surface finish, being applicable for different morphologies and sizes, while immersion is more focused on small elements with very complex geometries. Also a successful application of whole protections systems has been carried out, revealing good interactions between layers.
Characterisation of the coatings
This step was performed in Lurederra’s laboratory and saline mist chamber, INL facilities and TSF specific assessment. In this context, it took place the characterisation of the treated samples in terms of performances for each corrosion protection system, regarding adherence, corrosion resistance, hardness, among others. Complementary information has been generated related to microstructure, textures, defects and surface details.
The investigations showed promising results regarding corrosion protection, reaching to more than 4.200 hour of protection in saline mist chamber and successfully comply with corrosion aging test including exposure to salt spray in combination with UV, water condensation and freezing conditions according to ISO 12944-9.
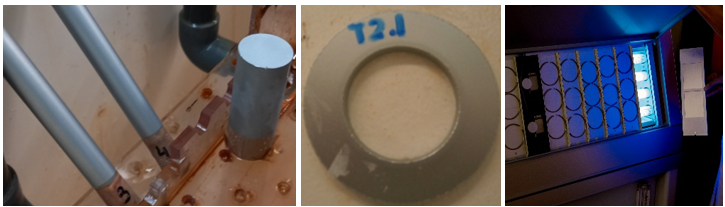