Developing strategies for new composite formulation
03 August 2022
Reinforced composites production and testing
The project plan outlines three strategies for new composite formulation:
- the use of nano-SiO2
- the use of Vitrimers/TPR recyclable resins
- the use of RCF
EIRE defined a preliminary material test matrix that is being used to test the initial epoxy-SiO2 resin formulations, developed by TWI, reinforced with glass fibre and a final material test matrix to generate a material datasheet for the chosen resin modified with nano-SiO2 and also the recyclable composites laminates produced by CETMA.
The use of nano-SiO2
Regarding the use of nano-SiO2 particles, TWI characterized and functionalized pyrogenic silica and Stöber silica powders. Next, TWI carried out a study on the viscosity versus loading behaviour of different silica powders in model resin in order to establish a pathway for silica incorporation procedure.
Upon the results of rheology study, ten modified samples were prepared for EIRE, five modified powder epoxy and five modified liquid epoxy resin samples with different loading ratios. For each of those samples, 1,3-dioxolane, a solvent selected based on Hansen Solubility Parameter (energetic) considerations, was used to reduce the inherent viscosity and facilitate mixing.
EIRE Manufactured preliminary test panels using the five initial powder epoxy-SiO2 and five initial epoxy-SiO2 infusion resin samples, prepared by TWI, reinforced with UD glass fibre. On the one hand, all 5 powder epoxy – SiO2 sample panels contained an unsatisfactory surface finish. It appears that the nano-SiO2 particles are incompatible with the powder epoxy process resulting in panels that contained substantial visual defects such as, dry fibres and lumps of dry nano-SiO2 particles scattered across the panels. This was most likely the effect of uncontrolled silica particles dispersion. Those panels were deemed unfit for testing and thus, powder epoxy-SiO2 developments were not selected as preferred strategy.
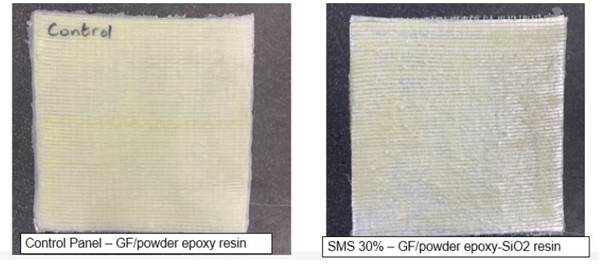
On the other hand, such dispersion problems were not associated with epoxy resin modification with 3 of the 5 epoxy-SiO2 infusion resin samples successfully infused, while the other 2 samples had a viscosity that was too high for the infusion process. EIRE carried out the preliminary material test matrix and the best performing epoxy-SiO2 infusion resin sample was chosen for the final material test matrix.
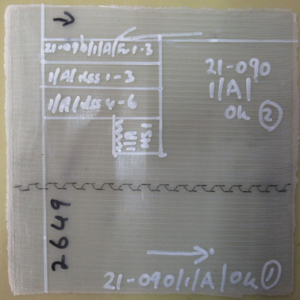
The use of Vitrimers/TPR recyclable resins
One of the project objectives states that MAREWIND will provide the design of new composites with intrinsic ability to be reprocessed and recycled, and that can also be easily processed using the same technologies used for thermosetting resin. The goal is to get a recyclable content in the composite above 40% of total. In respect to new recyclable resins, CETMA has carried out a commercial scouting to select the most suitable resin system for the wind industry in terms of physical and mechanical properties (durability and service temperature among others). Also, the composite matrix should be able to contemporary ensure recyclability requirements and suitable parameters for the intended infusion process.
Polymeric material developers’ attention is more and more focused on new types of recyclable polymer material: thermoplastics reactive resins (TPR) and vitrimers.
Based on results of preliminary material selection, it was found that industrial production of vitrimers is still under development, and among the scarce materials available to date, no commercial products were found with suitable properties for the infusion process defined, mainly regarding viscosity.
A new TPR (thermoplastic reactive resin) system Elium 188 XO, developend by Arkema has been successfully tested.
Apart from the main strategies studied, recyclable thermosets (RT) – epoxies in particular – were then investigated as an additional alternative related to recycling. The use of the cleavable amine hardener Recyclamine R101 (formerly developed and patented by Connora Technologies, USA and acquired in 2019 by Aditya Birla Chemicals, India) allows the recyclability of the matrix recovering both the clean fibers and a de-crosslinked epoxy (i.e. thermoplastic). Different epoxy resins have been preliminarily evaluated, then focusing the work on the standard system Gurit Prime 27 provided by EIRE with Recyclamine R101 hardener.
Thermal and rheological characterization of the above resins (TPR Elium 188XO and cleavable epoxy resin) were performed to analyse the reactivity of the systems, to set up the infusion parameters and also provide preliminary input data for the numerical model of such process.
The use of RCF
CETMA has set up the infusion process and manufactured composite laminates based on RCF and UD GF as reinforcements and TPR Elium and Recyclable Epoxy resin. Process optimization was performed in order to maximize the mechanical and physical properties and comparing them with traditional composite laminates based on GF and epoxy resin.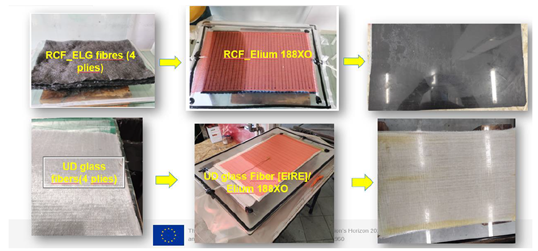
CETMA has defined the numerical model for the simulation of the resin infusion process in terms of the set-up, numerical parameters and the boundary conditions. The physical process is modelled by the Navier Stokes equations which in this case describes the mass, momentum and energy conservation of the resin flowing into a porous medium. To solve these equations the numerical method called FVM (Finite Volume Method) is used so far for the process optimization and will be used to optimize the infusion process on the full-scale demonstrator.
To solve these equations the numerical method called FVM (Finite Volume Method) is used. The model has shown great accuracy in simulating the resin flow in the infusion tests performed on small coupons and will be used to. to optimize the infusion process on the full-scale demonstrator. With regards to the thermo-mechanical recycling of TPR Elium 188XO with glass fiber laminates some preliminary tests have been done in order to evaluate the technical feasibility of these materials to be recycled and to be compression moulded, manufacturing two recycled flat panels.
CETMA has also developed a multi-scale numerical model to predict the macromechanical properties of the recycled materials based on RCF and Epoxy resin. Starting from the material properties of the composite constituents (fibres and matrix) and the microstructure characteristics (fibres volume fraction, fibres shape and orientation), a Representative Volume Element (RVE) of the composite material has been generated. A virtual characterization of RVE has been carried out to investigate the stiffness considering different loading conditions and the numerical results have been compared with the experimental ones. From the comparison was observed that the numerical results are in good agreement with the tensile modulus derived by experimental tests.
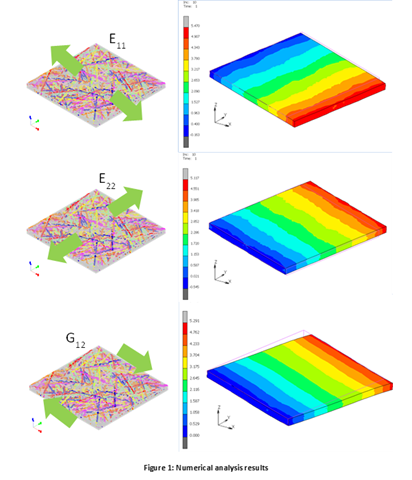