Developing a fouling-preventing coating for offshore submerged structures
03 August 2022
A fouling-preventing coating for different materials of offshore submerged structures has been developed and characterised at laboratory scale. In the first steps, two different base coatings were developed: low curing temperature and higher curing temperature.
The complete system, in both cases, implied a two-layer treatment, with a second thin layer focused in reducing the contact of the biological matter to the surface of the different materials. In the last months, based on a room temperature curing strategy, TECNAN and Lurederra developed a one layer system with oleo and hydrophobic final properties as the two other systems. All of these base matrixes and the one-layer system matrix, have similar colour, density, viscosity and stability overtime.
In addition, samples of materials with different chemical nature were selected in order to apply and validate the coating formulations. In particular, these materials are metal, painted metal and various polymers.
Applications of the antifouling coatings
The application selected was the spray gun because of its versatility for the target substrates. TECNAN has been working in the adjustment of the parameters such as the atomisation pressure, liquid flow and the fan width among others.
In the particular case of the hydrophobic properties, considering that the contact angle 90º is a good result reference, the values obtained of the different substrates tested in all the treatments developed, are quite inspiring.

In the case of the repellence of oil, very good results have been obtained too, not only in metal but also in polymeric substrates which have low reactivity and some initial repellence that imply a bigger challenge to generate a suitable and functional coating layer on it.
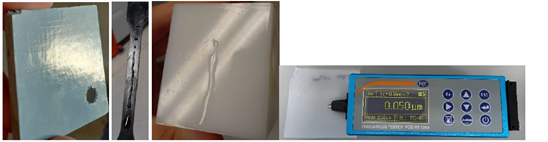
As a consequence, we could highlight the good results with the latest developed formulation based on one layer and low curing temperature, in relation with the adherence and compatibility with the substrates and the final repellence properties. The future work on the technologies validation and manufacturing, will be following this formulation strategy.
Tests in real environments
Enerocean in close cooperation with Lurederra and Tecnan, also defined and prepared the samples for the regulations ASTM D3623 and ASTM D5479, with the selected formulation ©. The materials selected for these tests were Nylon as the polymeric substrate and stainless steel as the metallic substrate. Enerocean was in charge of getting the samples and Lurederra of coating them with the protocols from Tecnan.
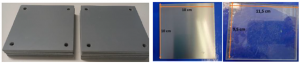
Evaluation of the coatings
EDF has carried out studies on the evaluation of the coatings. Currently, antifouling coatings are subjected to a series of conditions in order to be suitable for real applications and also, the performance must be determined by three properties:
- Ability to limit biofouling
- Low fouling adhesion and resistance of the coating to mechanical
- Chemical damages
Products belonging to the range of Chugoku Marine Paints have been selected in order to carry out comparative testing with the new solutions in development. These products consist of two different layers: ECOMAX Bi (base coat) and BIOCLEAN ECO (top coat), and it is based on non-biocidal technology. Lurederra and Tecnan have applied it and tested it on some substrates showing that the final thickness of the mentioned commercial product layers is quite significant meaning that the weight of the structures can increase in a considerable way, its appearance can change and the application can be extremely difficult.
