Novel solutions for improving the lifespan of the offshore wind farms
07 May 2021
Offshore wind turbines are often exposed to a variety of harsh conditions such as abrasion, bio-fouling, corrosion. These conditions seriously damage the components of the wind turbines. Moreover, due to the constant exposure of the marine moisture, splash and ice formations and based on the location of the windmill plan, some of the turbines have more severe damages. Overall, these conditions significantly decrease the lifespan of the wind turbines and limit the cost per MW.
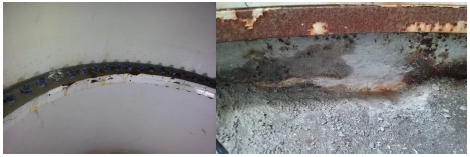
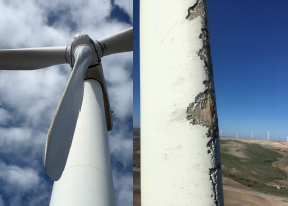
TACKLING CORROSION AND ABRASION
This gave birth to MAREWIND consortium – an EU funded-project that aims to resolve the major issues related to the short lifespan of the wind turbines. Firstly, the project will aim at improving coatings that will prevent leading-edge erosion, marine biofouling, biofouling-induced corrosion and corrosion (both splash and atmospheric). Moreover, MAREWIND project will optimize the concrete structures that go underneath the water surface. It will also improve in wind turbine blade performance (blades must show good mechanical properties).
TECHNICAL PROGRESS
In December 2020, MAREWIND project has started with creating a framework of requirements, references and a background of the parameters for each task (coatings duration, leading-edge protections, water resistance of the concretes developed). Secondly, the consortium also prepared a specific planning of technical activities for the rest of the project (characterisations to be carried out, lab-scale tests, scale up processes, etc.).
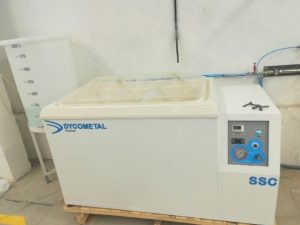
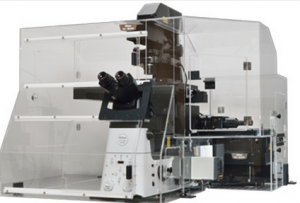
MAREWIND DEMO SITES
During MAREWIND project, the project partners will develop project technologies for anti-corrosion coatings for metallic parts and fastening elements, anti-fouling coatings, new composites for blades, anti-erosion coatings for the blades and new high-performance concrete materials. These technologies will be tested on different demonstration sites. The selected demonstration sites have been selected as follow:- The Port of Leixões: It is the second busiest port in Portugal. It represents 25% of all Portuguese international commercial trading. The port is located in the north of the country and it has 120 ha of water area. This is a possible site for the GBS prototype.
- Aguçadoura Offshore Test Site: it is located in Northern Portugal where the WindFloat wind turbine is installed among other projects. The installation site is located 6 km off from Aguçadoura beach and has 50 m water depth. This is considered to be a possible site for the GBS prototype.
- EDF operated Offshore Wind farms: Two farms are available at Blyth and Teesside in the United Kingdom. MAREWIND will be given access to the farms in order to test anti corrosion coatings on coupons in real environmental conditions.
- Eumer’s facilities: as CETMA partner, they are part of the University of Salento and they are located in the Ecotekne campus in Lecce. They count with a multi-element wavemaker to perform physical model tests in a controlled environment and under operational and extreme conditions. Concrete project solutions that are to be developed will be tested in this site to evaluate the effect of the wave motion on the developed concrete structures.
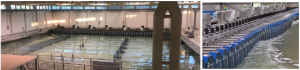